Решения
Промышленная линия по производству тостового хлеба производит различные виды тостового хлеба. Производственная мощность немного варьируется в зависимости от веса хлеба. В настоящее время эта производственная линия может производить 4500 штук хлеба весом 900-1000 граммов в час.
Our self-developed multi-functional automatic biscuit production line, with advanced technology and intelligent design, is committed to meet the core demand of the global baking industry for efficient, hygienic and diversified production. The production line can flexibly produce tough cookies, crispy cookies, soda cookies and other categories, adapting to different formulas and technological requirements, which is the ideal choice for small and medium-sized food enterprises to upgrade production capacity and enhance competitiveness.
Автоматическая линия для производства булочек для бургеров IMAR представляет собой всеобъемлющую производственную систему, которая может обеспечить быстрое и эффективное производство значительных объемов гамбургеров. Широко применяемая в различных коммерческих и промышленных средах, эта передовая система находит широкое применение в крупных ресторанах быстрого обслуживания, супермаркетах, а также на предприятиях по производству продуктов питания.
В Rusk Bread Production Line delivers industrial-scale versatility, engineered to seamlessly transition from artisanal mid-size bakeries to high-capacity industrial facilities. With outputs scaling from 200 to 1000 kg/hour
IMAR EQUIPMENT CO., LTD
ЧТО МЫ ДЕЛАЕМ?
IMAR Equipment Co., Ltd. is an enterprise specializing in the manufacturing of baking machinery. Such as full automatic biscuit line, bread line, cake line, wafer line with flour dosing systems. The company has a team of engineers with rich experience in baking machinery design and on-site construction. In addition, retired experts outstanding in the industry are reemployed as the company’s advisory team to enhance project delivery capabilities. After more than ten years of industry precipitation and accumulation, the company’s products are not only sold well in the domestic market but also exported to many countries such as Bangladesh in Asia, Uzbekistan, Kazakhstan, Kuwait, Sudan and Algeria in Africa, Jamaica and Bolivia in America.
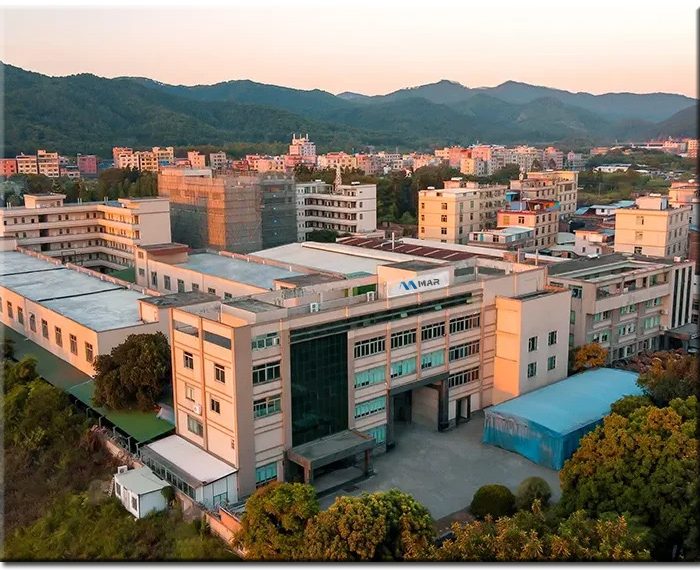
НОВОСТИ
Для руководителей международных пищевых конгломератов, новаторских централизованных кухонь или амбициозных сетей пекарен выбор поставщика линий для производства печенья — это не просто покупка оборудования, а стратегический шаг к масштабируемости, эффективности и глобальной конкурентоспособности вашего бренда. В отрасли, где простой обходится в миллионы, а стабильность — превыше всего, партнёрство с действительно элитным глобальным поставщиком комплексных линий для производства печенья — это непреложный факт.
Однако, ориентируясь на мировом рынке, мы обнаруживаем разительные контрасты. Многие заявляют о своих возможностях, но лишь немногие обеспечивают инженерную глубину, операционную устойчивость и международную инфраструктуру поддержки, необходимые производителям продуктов питания из списка Fortune 500. Будучи ведущим китайским новатором в области промышленных линий для производства печенья, работающим с более чем 20 всемирно известными брендами (включая гигантов отрасли), мы, IMAR Equipment, поняли, что отличает транзакционных поставщиков от партнеров-трансформаторов.
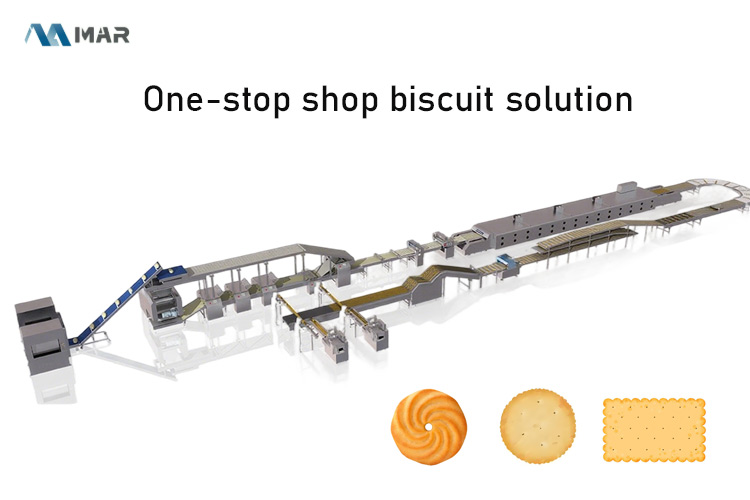
Почему «все в одном месте» — единственно жизнеспособная стратегия промышленного производства печенья
Разрозненность поставок — сочетание экструдеров из Италии, печей из Германии и упаковочных линий из Японии — создаёт кошмар из-за задержек интеграции, технической несовместимости и перекладывания вины во время кризисов. Настоящие готовые решения для производства печенья требуют единой ответственности.
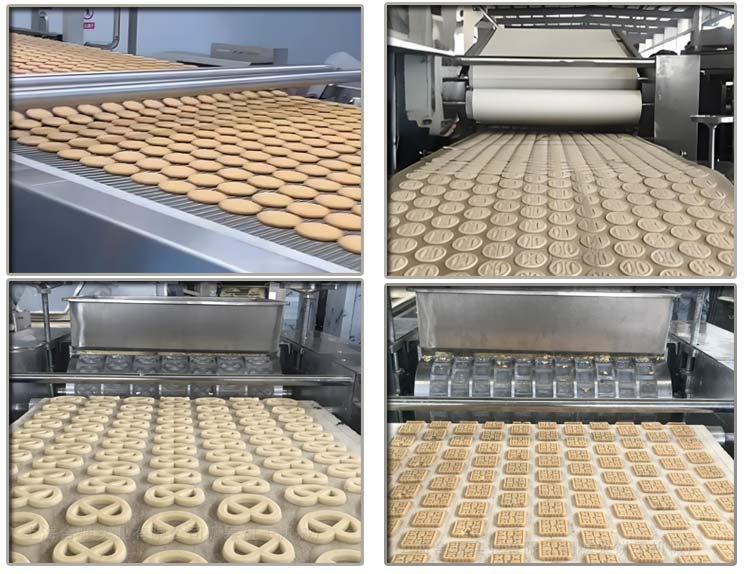
Наши основные отличия как вашего ведущего мирового поставщика:
☆Непревзойденная вертикальная интеграция:
Передовое производственное предприятие площадью 10 000 м² в Гуанчжоу, Китай, оснащенное обрабатывающими центрами с ЧПУ, роботизированной сваркой и сборочными участками, соответствующими стандартам чистой комнаты ISO.
☆Сквозной контроль: от НИОКР и точного изготовления формовочных роликов, режущих головок и ленточных конвейеров до программирования ПЛК и окончательных заводских приемочных испытаний (FAT).
☆Результат: Гармоничная работа системы, на 20 % более быстрая установка по сравнению с модульным снабжением, прослеживаемость компонентов на протяжении всего срока службы.
☆Проверенный масштаб для мировых гигантов:
Разработаны линии производительностью 200–1500 кг/час крекеров, затяжного печенья, сэндвич-печенья и изделий ротационного формования.
Прямая ссылка: Поставка полностью автоматизированной линии гибридной туннельной печи длиной 22 метра для завода 10-й крупнейшей в мире компании по производству снеков на Среднем Западе США (2023 г.), с достижением 99% времени бесперебойной работы в первый год.
Портфолио: высокоскоростная проволочная резка, ротационное формование, ламинирование твердого теста, экструзия мягкого теста — все это можно настроить для рецептов без глютена, с высоким содержанием клетчатки или с низким содержанием сахара.
☆Инновации, основанные на инженерных разработках, а не имитация:
Специализированный центр технологий производства печенья с пилотными линиями для совместной разработки рецептур и моделирования производительности.
Фокус: Экономия энергии (до 20% по сравнению со старыми духовками)
☆Глобальная инфраструктура поддержки – ваша оперативная сеть безопасности:
Многоязычная поддержка 48/7/365: выездные инженеры, прошедшие обучение у OEM-производителей, а не сторонние подрядчики. Доставка критически важных запасных частей по всему миру осуществляется в течение 72 часов.
☆Compliance Without Compromise:
Сертификации, выходящие за рамки основных: соответствие стандартам CE, UL, NSF. Интегрированная конструкция HACCP.
Целостность материалов: контактирующие с пищевыми продуктами поверхности из нержавеющей стали 304/316L, уплотнения/смазочные материалы, соответствующие требованиям FDA, полная сертификация материалов (MTC).
☆Лидерство по совокупной стоимости владения (TCO):
За пределами наклейкой цены: 20-летнее проектирование жизненного цикла, модульные модернизации (задел на будущее), отчеты по моделированию энергопотребления.
Задокументированные результаты: Клиенты сообщают о снижении операционных расходов на 18–23 % по сравнению с европейскими аналогами за 5 лет за счет экономии энергии, сокращения отходов и повышения эффективности технического обслуживания.
Скрытые затраты при выборе поставщика линии печенья «Me Too»
Многие производители предлагают внешне похожие машины. Риски возникают после установки:
Ошибки интеграции: несоответствия механической части и управления, приводящие к потерям мощности на 15–30 %.
Кошмары несоответствия: отклонение поставок из-за ненадлежащей документации или несоответствующих материалов.
Перебои в подаче электроэнергии: время реагирования более 12 часов, неподготовленные местные специалисты, непомерные наценки на запасные части.
Негибкость рецептур: линии не способны адаптироваться к новым рецептурам без дорогостоящей модернизации.
Оборудование IMAR: мы ваш стратегический партнер по производству печенья
Для вас мы поставляем больше, чем просто машины:
Лаборатории совместных инноваций: совместная разработка продуктов нового поколения (например, печенья на растительной основе, функциональных ингредиентов).
Анализ рынка: информация о региональных вкусовых предпочтениях, тенденциях упаковки, изменениях в регулировании.
Доступ к сети: знакомство с поставщиками ингредиентов и партнерами по упаковке в рамках нашей глобальной экосистемы.
Вердикт мировых лидеров:
“After evaluating 7 suppliers globally, IMAR Equipment presented the only truly integrated solution. Their 1000 kg/hr line in our *** facility exceeded ramp-up targets by 3 weeks. The predictive maintenance system prevented a €150k bearing failure in Month 2.”* — Global Operations Director, Top 3 European Biscuit Brand
“Their understanding of our requirements for our US expansion in bakery business was unparalleled. The turnkey delivery, including local compliance sign-off, removed massive execution risk.” — CTO, Asian Snack Conglomerate
Займите лидирующие позиции в производстве печенья
Гонка за эффективностью, инновациями и глобальной гибкостью не терпит отлагательств. Сотрудничайте с поставщиком, чьи возможности доказаны на самых высоких уровнях промышленного производства продуктов питания.
[IMAR Equipment]: Where Global Scale Meets Precision Execution.
One Partnership. One Source. Infinite Biscuit Possibilities.
In the high-speed manufacturing industry, industrial baking ovens have become an indispensable core equipment in the baking industry. These machines are designed for high-volume, high-temperature precision processing and are the cornerstone of production consistency, efficiency and safety. For companies, investing in industrial ovens is no longer a luxury option, but a strategic necessity to increase production capacity. However, choosing an industrial oven is only the starting point. Choosing a professional and reliable industrial baking oven supplier is the key to success. The professionalism of the supplier directly affects the performance, service life and ultimate return on investment (ROI) of the equipment. This article will explore the core value of industrial ovens and focus on the core factors that must be considered when choosing an industrial oven supplier.
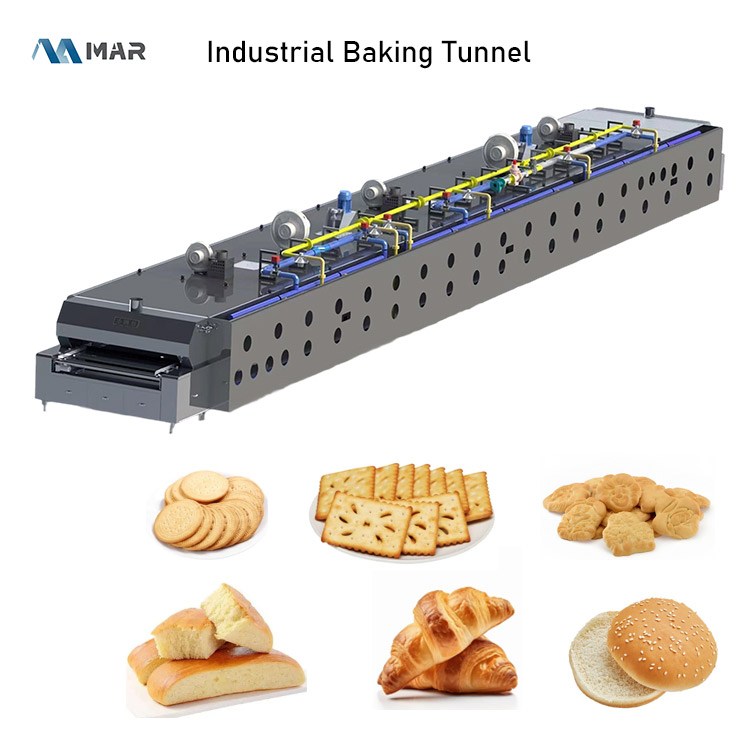
- How do industrial oven suppliers help the baking industry?
Industrial ovens are designed to meet the rigorous needs of large-scale production, and they bring advantages far beyond traditional or small equipment. The solutions provided by excellent industrial oven suppliers can bring significant changes to manufacturers for the following reasons:
⭕Improve efficiency and capacity: The equipment provided by professional industrial oven suppliers is designed for continuous high-intensity operation and can efficiently process thousands of products per hour. Its advanced heating system (convection, infrared or hybrid technology) ensures that heat is quickly and evenly distributed, greatly shortening the production cycle and improving overall productivity.
⭕Ensure accuracy and consistency: Unlike home ovens, high-quality industrial oven suppliers supply equipment equipped with precision temperature control, humidity regulation and airflow management systems. This accuracy is crucial for baked goods such as bread, cookies, pizza, cakes, etc., and is the core guarantee of stable product quality.
⭕Achieve long-term cost savings: Although industrial ovens require high initial investment, reliable industrial oven suppliers will provide energy-saving, efficient, durable and low-maintenance equipment, significantly reducing long-term operating costs. Automation functions (such as programmable recipes and remote monitoring) further reduce manual dependence and operational errors, saving costs.
⭕Ensure worry-free compliance: Responsible industrial oven suppliers ensure that their equipment strictly complies with industry safety and regulatory standards such as CE, UL, and FDA. Choosing them means that your production compliance is guaranteed and the risk of fines and recalls is effectively avoided.
⭕Provide scalability and flexibility: Forward-looking industrial oven suppliers usually provide modular design oven solutions, allowing companies to easily expand production capacity or adapt new product lines without large-scale transformation. This flexibility is of great strategic value in a dynamic market with changing demands.
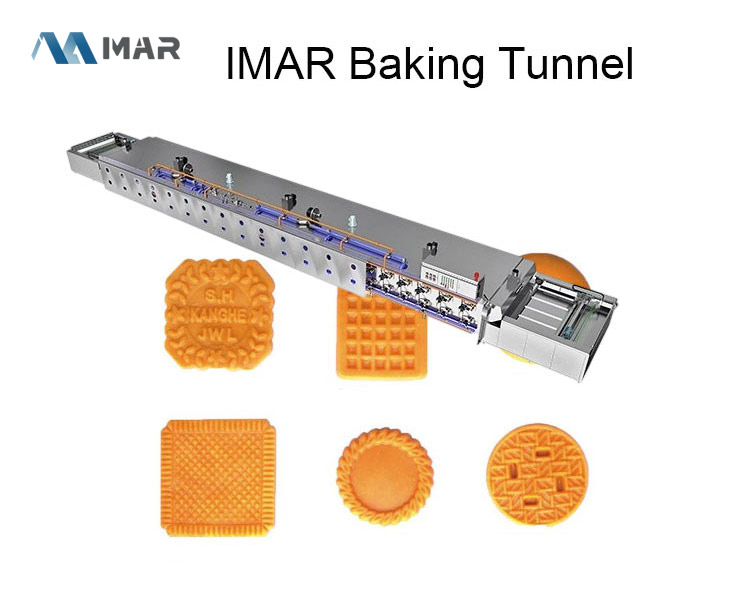
- Evaluate Your Needs: Identify the Right Baking Oven for Your Application
Before selecting a supplier, be sure to conduct a thorough needs assessment. The ideal industrial oven for your business depends on several factors:
Production volume: Consider your current production volume and future growth projections. Suppliers should offer ovens in a variety of sizes, from batch processors to continuous conveyor systems, to meet your needs.
Energy efficiency: Look for ovens with energy-saving features, such as heat recovery systems, insulation upgrades, or alternative fuel options (e.g., gas or electric). This not only reduces operating costs, but also meets sustainability goals.
Customization requirements: Some applications require custom solutions, such as specialized grills, multi-zone heating, or. Make sure your supplier is able to make modifications without compromising performance.
Budget constraints: While cost should not be the only determining factor, balancing quality and price is critical. Request a detailed quote that includes installation, training, and after-sales support.
By clarifying these parameters, you will be better able to communicate your needs to potential suppliers and avoid costly mismatches.
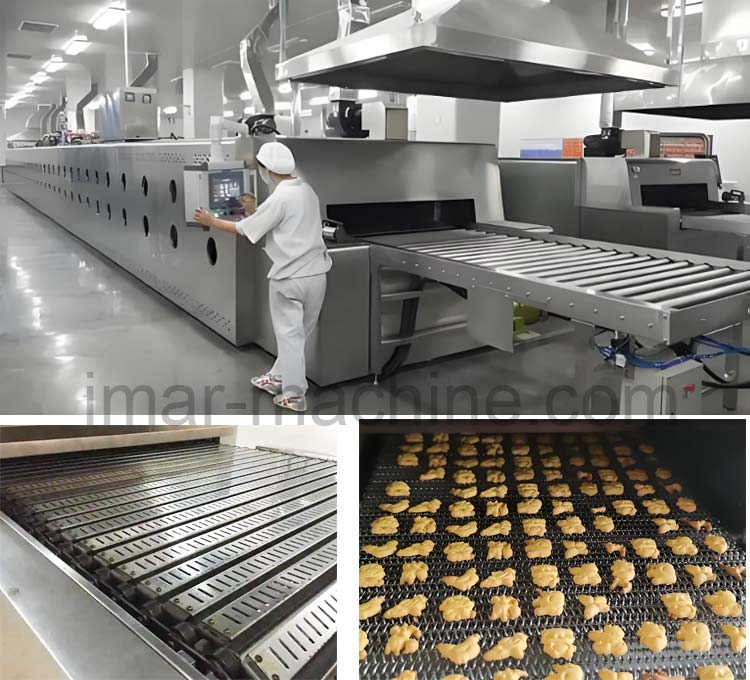
- Key Factors for Selecting an Industrial Baking Oven Supplier
Choosing the right supplier is as critical as selecting the oven itself. Here’s what to evaluate:
Experience and Industry Expertise: Opt for a supplier with a proven track record in your specific industry. An experienced partner will understand your challenges and recommend solutions tailored to your application.
Product Range and Innovation: A diverse product portfolio indicates a supplier’s ability to adapt to evolving technologies.
Quality and Certifications: Verify that the supplier adheres to international standards (e.g., ISO 9001) and that their ovens carry relevant certifications. Ask for case studies or client testimonials to gauge real-world performance.
After-Sales Support and Service: A reliable supplier offers comprehensive post-purchase support, including installation, operator training, spare parts availability, and 24/7 technical assistance. Prompt service minimizes downtime — a critical factor in production environments.
Sustainability Initiatives: In an era of eco-conscious manufacturing, partner with suppliers committed to sustainability. This could include using recyclable materials, reducing emissions, or offering energy-efficient upgrades.
Video of Industrial Baking Tunnel Oven:
Choosing an industrial oven and its supplier is a decision that will impact your business for years to come. With nearly 20 years of experience exporting industrial baking equipment, we at Imar Machine are able to prioritize efficiency, quality, and long-term partnerships. Choosing us is not just buying equipment, but investing in a strategic ally to help your business thrive in a competitive market. Remember, the cheapest option is not always the best; look for a supplier who aligns with your values, understands your needs, and is committed to your success. Make the right choice, and your industrial oven will become the cornerstone of your production excellence.
The global soda biscuit market is experiencing unprecedented growth, driven by consumer preferences shifting toward healthier snacking options. According to a report by Market Research Future, the soda cracker industry is expected to grow at a compound annual growth rate of 7.8% by 2030, driven by the growing demand for low-sugar, high-fiber and clean-label products. As disposable incomes rise in emerging economies, convenient foods like soda crackers are becoming a must-have in people’s kitchens.
However, meeting this demand requires more than just recipes, but also precision, efficiency and scalability in production. Manual operations often lead to inconsistencies in texture, thickness and baking quality, which directly affects brand reputation. This is where advanced soda biscuit processing machine becomes indispensable. We IMAR Equipment offers complete soda biscuit processing machine. By automating mixing, laminating, forming and baking, manufacturers can achieve standardized production, reduce labor costs, and seamlessly scale their business.
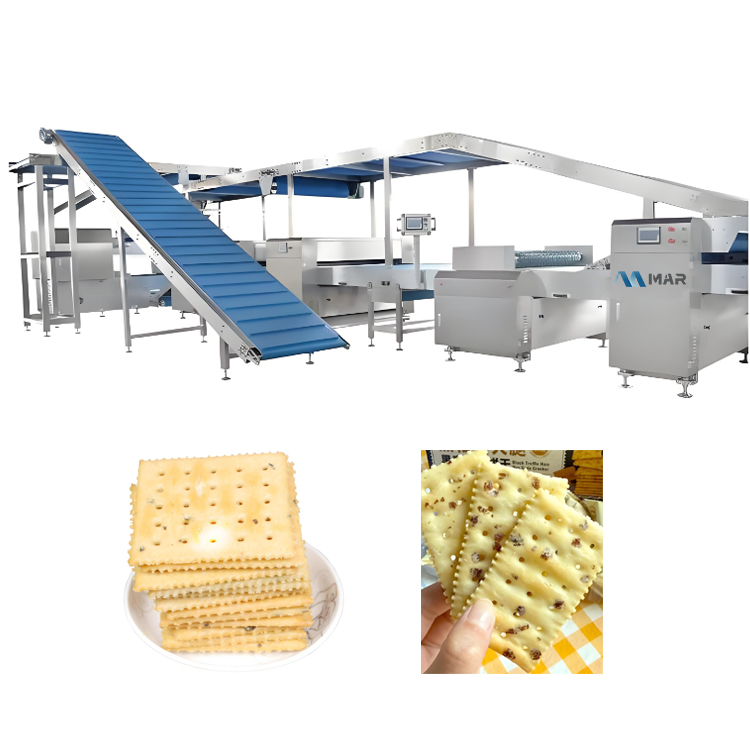
As a trusted supplier of soda biscuit processing machine, we understand the key role technology plays in transforming raw materials into the crispy, golden crackers that the world loves. Let’s explore the excellence of soda biscuit machinery and how to partner with the right supplier to future-proof your business.
What Makes a High-Quality Soda Biscuit Machine?
Investing in a biscuit baking industry is a long-term decision that affects product quality, operating costs, and scalability. Here are the three advantages of a quality machine:
⚪Precision temperature control system
Soda biscuits rely on precise fermentation and baking to achieve their signature crispy taste and fluffy layers. Advanced machines use multi-zone temperature control (accuracy ±1°C) to optimize dough relaxation, layering, and baking. For example, uneven heat distribution can cause cracks or underbaked centers – and our tunnel ovens eliminate these problems by adjusting the temperature in real time based on humidity sensors.
⚪Customizable molds
High-quality machines offer interchangeable molds to meet the needs of different thicknesses (1-5 mm) and designs (diamond, round, or branded shapes). Modular mold systems can be quickly changed without downtime, allowing producers to easily diversify their product lines.
⚪Energy-saving design
Modern machines have integrated heat recovery systems that can use waste heat to preheat dough or heat equipment, reducing energy consumption by up to 25%. In addition, the servo drive motor reduces power consumption by 30% compared to conventional gear systems, ensuring that energy-saving and consumption-reduction targets are met.
Video of Soda biscuit production line:
Why Partner with IMAR Machine? Core Competencies of a Trusted Supplier
Choosing the right machinery supplier is not just about technical specifications, but also about collaboration, expertise and reliability. Here are our advantages:
20+ Years of Industry Leadership
With more than two decades of experience in baking equipment manufacturing, we have continuously refined our solutions through cooperation with global giants such as Garden, Britannia, etc. Our equipment has produced billions of cookies in more than 20 countries, and its durability and excellent performance are trusted by customers.
Tailor-made solutions to meet the needs of all sizes
Whether you are a startup or a multinational company, our equipment can meet your needs. Our flexible line processing capacity ranges from 200 kg/hour for niche artisanal brands to 2000kg/hour for mass-market enterprises. Our engineers will customize the workflow without compromising speed.
Trustworthy Certifications
Compliance is crucial in food production. Our machines have CE, FDA and HACCP certifications, ensuring compliance with hygiene, safety and traceability standards. From easy-to-sterilize stainless steel surfaces to allergen isolation solutions, our designs always keep food safety in mind.
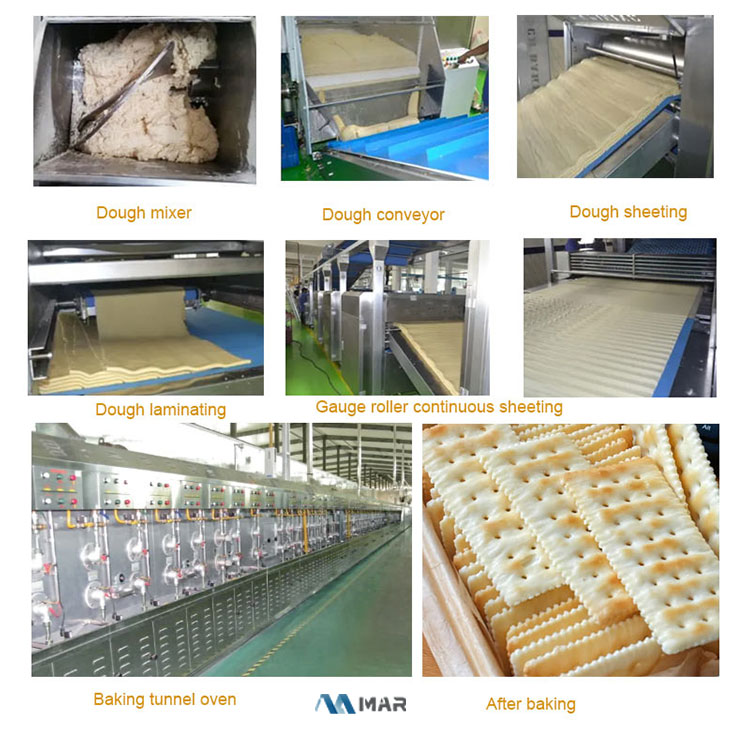
Solving Your Biggest Challenges in Soda Biscuit Production
Even with the best recipes, producers face persistent hurdles. Here’s how we tackle them:
Problem 1: Inconsistent Dough Elasticity
Variations in flour quality or humidity can ruin dough structure. Our patented kneading technology uses real-time viscosity sensors to adjust mixing speed and water ratios, ensuring uniform gluten development every time.
Problem 2: Fragile Finished Products
Brittle biscuits often result from improper baking or cooling. Our humidity-adaptive baking tunnels maintain optimal moisture levels during cooling, while anti-vibration conveyor belts prevent breakage.
Problem 3: High Energy Bills
Traditional ovens waste energy. Our AI-powered Energy Saver Mode analyzes production schedules and automatically switches to idle during low-demand periods, slashing costs by 18–22%.
Beyond the sale: Lifetime support for ongoing success
Our commitment begins when the machine is installed—not ends.
Comprehensive training and maintenance
We provide free on-site training for operators and technicians, covering troubleshooting, sanitation and minor repairs. Customers also receive a personalized annual maintenance plan, including wear diagnostics and software updates.
Case study: 30% reduction in downtime
A Middle Eastern customer was experiencing frequent breakdowns due to desert dust clogging their motors. After implementing our modular airflow redesign and scheduled filter changes, their annual downtime was reduced from 14 days to 9.8 days, saving $220,000 in lost production.
Ready to Boost Your Production? Let’s Build Your Success Story!
The soda biscuit market waits for no one. Whether you’re upgrading existing lines or launching a new brand, our team is here to help you produce faster, smarter, and greener.
Act Now and Unlock Exclusive Benefits:
🎁 Free Production Line Audit: Our experts will identify efficiency gaps and recommend solutions.
🎁 Limited-Time Bonus: The first 20 inquiries receive a VIP Maintenance Handbook and 10 Proven Soda Biscuit Recipes (including low-carb and vegan options).
Contact us today to schedule a consultation. Together, let’s turn your vision into the world’s next favorite soda biscuits!
IMAR EQUIPMENT CO., LTD
АДРЕС
№6 Инсинь-роуд, улица Лундун, район Тяньхэ, Гуанчжоу
Электронная почта
imar@topbakings.com
ТЕЛЕФОН
+86 13027764560