SOLUTIONS
The industrial toast bread production line produce different types of toast bread. The production capacity varies slightly depending on the weight of the bread. Currently, this production line can produce 4,500 pieces of 900-1,000 grams bread per hour.
Our self-developed multi-functional automatic biscuit production line, with advanced technology and intelligent design, is committed to meet the core demand of the global baking industry for efficient, hygienic and diversified production. The production line can flexibly produce tough cookies, crispy cookies, soda cookies and other categories, adapting to different formulas and technological requirements, which is the ideal choice for small and medium-sized food enterprises to upgrade production capacity and enhance competitiveness.
IMAR automatic burger bun production line represents an all – encompassing production system, which can facilitate the rapid and efficient production of substantial quantities of hamburgers. Widely adopted in various commercial and industrial environments, this advanced system finds extensive use in large – scale quick – service restaurants, supermarkets, as well as food manufacturing plants.
The Rusk Bread Production Line delivers industrial-scale versatility, engineered to seamlessly transition from artisanal mid-size bakeries to high-capacity industrial facilities. With outputs scaling from 200 to 1000 kg/hour
IMAR EQUIPMENT CO., LTD
WHAT WE DO?
IMAR Equipment Co., Ltd. is an enterprise specializing in the manufacturing of baking machinery. Such as full automatic biscuit line, bread line, cake line, wafer line with flour dosing systems. The company has a team of engineers with rich experience in baking machinery design and on-site construction. In addition, retired experts outstanding in the industry are reemployed as the company’s advisory team to enhance project delivery capabilities. After more than ten years of industry precipitation and accumulation, the company’s products are not only sold well in the domestic market but also exported to many countries such as Bangladesh in Asia, Uzbekistan, Kazakhstan, Kuwait, Sudan and Algeria in Africa, Jamaica and Bolivia in America.
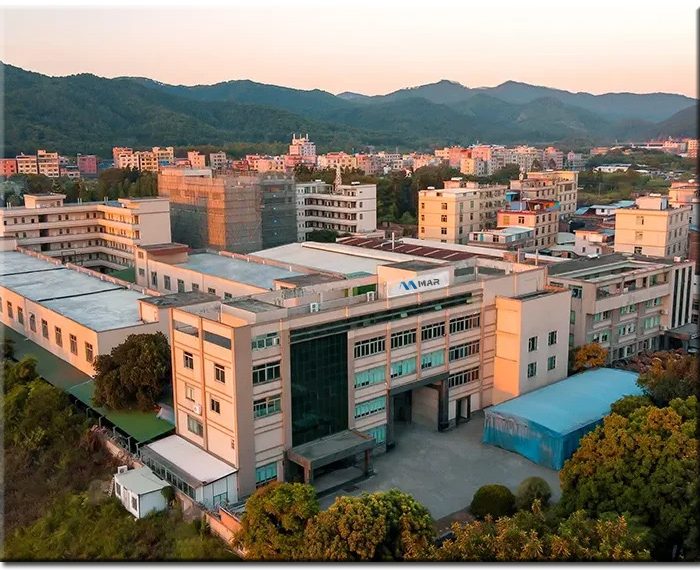
NEWS
For executives steering multinational food conglomerates, pioneering central kitchens, or ambitious bakery chains, the choice of a biscuit production line supplier isn’t just an equipment purchase—it’s a strategic commitment to your brand’s future scalability, efficiency, and global competitiveness. In an industry where downtime costs millions and consistency is king, partnering with a truly elite One-stop Biscuit Lines Global Supplier is non-negotiable.
Yet, navigating the global marketplace reveals stark contrasts. While many claim capability, few deliver the engineering depth, operational resilience, and international support infrastructure demanded by Fortune 500 food producers. As China’s foremost industrial biscuit line innovator, serving over 20+ globally recognized brands (including industry titans), we IMAR Equipment has decoded what separates transactional vendors from transformative partners.
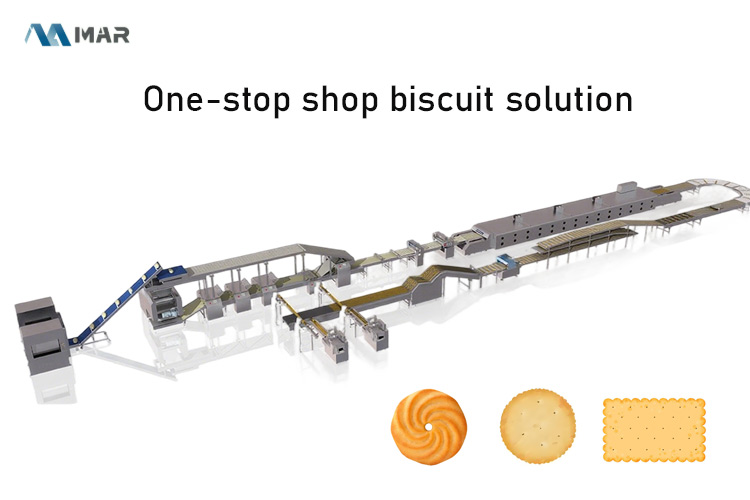
Why “One-Stop” is the Only Viable Strategy for Industrial-Scale Biscuit Production
Fragmented sourcing—mixing extruders from Italy, ovens from Germany, and packaging lines from Japan—creates a nightmare of integration delays, technical incompatibilities, and finger-pointing during crises. True turnkey biscuit solutions demand unified accountability.
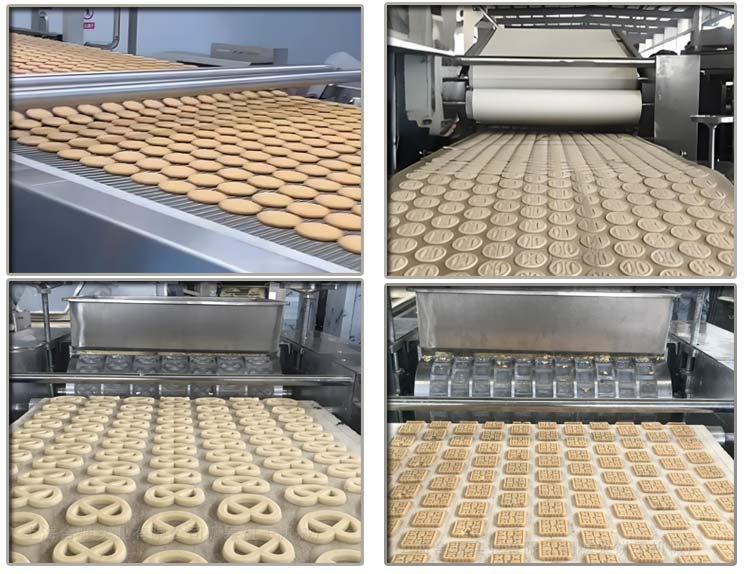
Our Core Differentiators as Your Premier Global Supplier:
☆Unmatched Vertical Integration:
10000㎡ advanced manufacturing facility in Guangzhou China, featuring CNC machining centers, robotic welding, and ISO clean-room assembly bays.
☆End-to-end control: From R&D and precision fabrication of forming rolls, cutting heads, and oven bands to PLC programming and final FAT (Factory Acceptance Testing).
☆Result: Seamless system harmony, 20% faster installation vs. modular sourcing, lifetime traceability of components.
☆Proven Scale for Global Giants:
Engineered lines producing 200 –1500 kg/hour of crackers, hard biscuits, sandwich cookies, and rotary moulded varieties.
Direct Reference: Supplied a fully automated, 22-meter hybrid tunnel oven line for a Top 10 global snack company’s Midwest USA plant (2023), achieving 99% uptime in first year.
Portfolio: High-speed wire-cut, rotary moulding, laminating for hard dough, soft dough extrusion – all configurable for gluten-free, high-fiber, or low-sugar recipes.
☆Engineering-Led Innovation, Not Imitation:
Dedicated Biscuit Technology Center with pilot lines for recipe co-development and throughput simulation.
Focus: Energy reduction (up to 20% vs. legacy ovens)
☆Global Support Infrastructure – Your Operational Safety Net:
48/7/365 Multilingual Support: Field engineers with OEM training, not third-party contractors. Critical spares air-shipped within 72 hours globally.
☆Compliance Without Compromise:
Certifications Beyond Basics: CE, UL, NSF compliance standard. HACCP-integrated design.
Material Integrity: 304/316L stainless steel food contact surfaces, FDA-compliant seals/lubricants, full material certifications (MTC).
☆Total Cost of Ownership (TCO) Leadership:
Beyond Sticker Price: 20-year lifecycle engineering, modular upgrades (future-proofing), energy modeling reports.
Documented Outcomes: Clients report 18-23% lower OPEX versus European equivalents over 5 years via energy savings, reduced waste, and maintenance efficiency.
The Hidden Costs of Choosing a “Me-Too” Biscuit Line Supplier
Many manufacturers offer superficially similar machines. The risks emerge post-installation:
Integration Failures: Mechanical/control mismatches causing 15-30% capacity gaps.
Compliance Nightmares: Rejection of shipments due to inadequate documentation or non-conforming materials.
Support Blackouts: 12+ hour response times, untrained local technicians, exorbitant spare parts markups.
Recipe Inflexibility: Lines unable to adapt to new formulations without costly retrofits.
IMAR Equipment: We Are Your Strategic Biscuit Production Partner
For you, we deliver more than machines:
Co-Innovation Labs: Joint development of next-gen products (e.g., plant-based biscuits, functional ingredients).
Market Intelligence: Insights on regional taste profiles, packaging trends, regulatory shifts.
Network Access: Introductions to ingredient suppliers, packaging partners within our global ecosystem.
The Verdict from Global Leaders:
“After evaluating 7 suppliers globally, IMAR Equipment presented the only truly integrated solution. Their 1000 kg/hr line in our *** facility exceeded ramp-up targets by 3 weeks. The predictive maintenance system prevented a €150k bearing failure in Month 2.”* — Global Operations Director, Top 3 European Biscuit Brand
“Their understanding of our requirements for our US expansion in bakery business was unparalleled. The turnkey delivery, including local compliance sign-off, removed massive execution risk.” — CTO, Asian Snack Conglomerate
Claim Your Position at the Forefront of Biscuit Manufacturing
The race for efficiency, innovation, and global agility won’t wait. Partner with a supplier whose capabilities are proven at the highest tiers of industrial food production.
[IMAR Equipment]: Where Global Scale Meets Precision Execution.
One Partnership. One Source. Infinite Biscuit Possibilities.
In the high-speed manufacturing industry, industrial baking ovens have become an indispensable core equipment in the baking industry. These machines are designed for high-volume, high-temperature precision processing and are the cornerstone of production consistency, efficiency and safety. For companies, investing in industrial ovens is no longer a luxury option, but a strategic necessity to increase production capacity. However, choosing an industrial oven is only the starting point. Choosing a professional and reliable industrial baking oven supplier is the key to success. The professionalism of the supplier directly affects the performance, service life and ultimate return on investment (ROI) of the equipment. This article will explore the core value of industrial ovens and focus on the core factors that must be considered when choosing an industrial oven supplier.
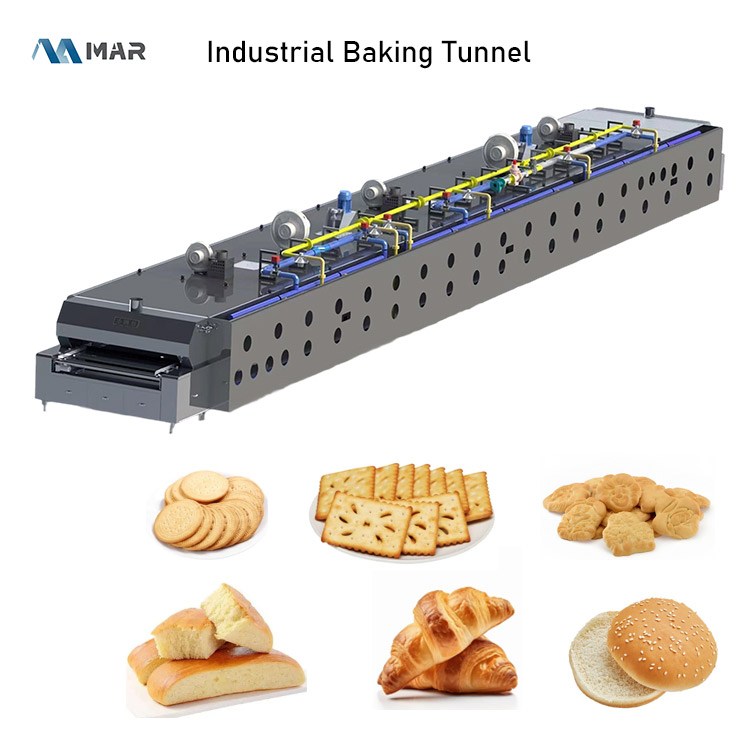
- How do industrial oven suppliers help the baking industry?
Industrial ovens are designed to meet the rigorous needs of large-scale production, and they bring advantages far beyond traditional or small equipment. The solutions provided by excellent industrial oven suppliers can bring significant changes to manufacturers for the following reasons:
⭕Improve efficiency and capacity: The equipment provided by professional industrial oven suppliers is designed for continuous high-intensity operation and can efficiently process thousands of products per hour. Its advanced heating system (convection, infrared or hybrid technology) ensures that heat is quickly and evenly distributed, greatly shortening the production cycle and improving overall productivity.
⭕Ensure accuracy and consistency: Unlike home ovens, high-quality industrial oven suppliers supply equipment equipped with precision temperature control, humidity regulation and airflow management systems. This accuracy is crucial for baked goods such as bread, cookies, pizza, cakes, etc., and is the core guarantee of stable product quality.
⭕Achieve long-term cost savings: Although industrial ovens require high initial investment, reliable industrial oven suppliers will provide energy-saving, efficient, durable and low-maintenance equipment, significantly reducing long-term operating costs. Automation functions (such as programmable recipes and remote monitoring) further reduce manual dependence and operational errors, saving costs.
⭕Ensure worry-free compliance: Responsible industrial oven suppliers ensure that their equipment strictly complies with industry safety and regulatory standards such as CE, UL, and FDA. Choosing them means that your production compliance is guaranteed and the risk of fines and recalls is effectively avoided.
⭕Provide scalability and flexibility: Forward-looking industrial oven suppliers usually provide modular design oven solutions, allowing companies to easily expand production capacity or adapt new product lines without large-scale transformation. This flexibility is of great strategic value in a dynamic market with changing demands.
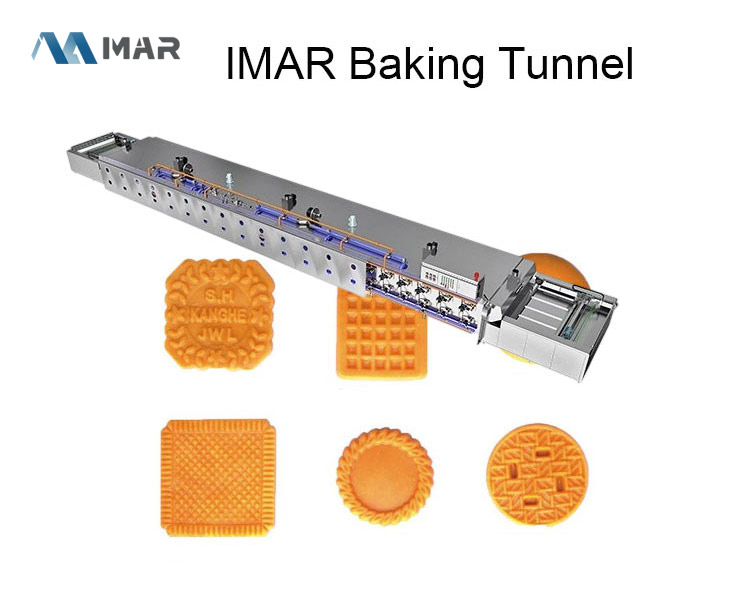
- Evaluate Your Needs: Identify the Right Baking Oven for Your Application
Before selecting a supplier, be sure to conduct a thorough needs assessment. The ideal industrial oven for your business depends on several factors:
Production volume: Consider your current production volume and future growth projections. Suppliers should offer ovens in a variety of sizes, from batch processors to continuous conveyor systems, to meet your needs.
Energy efficiency: Look for ovens with energy-saving features, such as heat recovery systems, insulation upgrades, or alternative fuel options (e.g., gas or electric). This not only reduces operating costs, but also meets sustainability goals.
Customization requirements: Some applications require custom solutions, such as specialized grills, multi-zone heating, or. Make sure your supplier is able to make modifications without compromising performance.
Budget constraints: While cost should not be the only determining factor, balancing quality and price is critical. Request a detailed quote that includes installation, training, and after-sales support.
By clarifying these parameters, you will be better able to communicate your needs to potential suppliers and avoid costly mismatches.
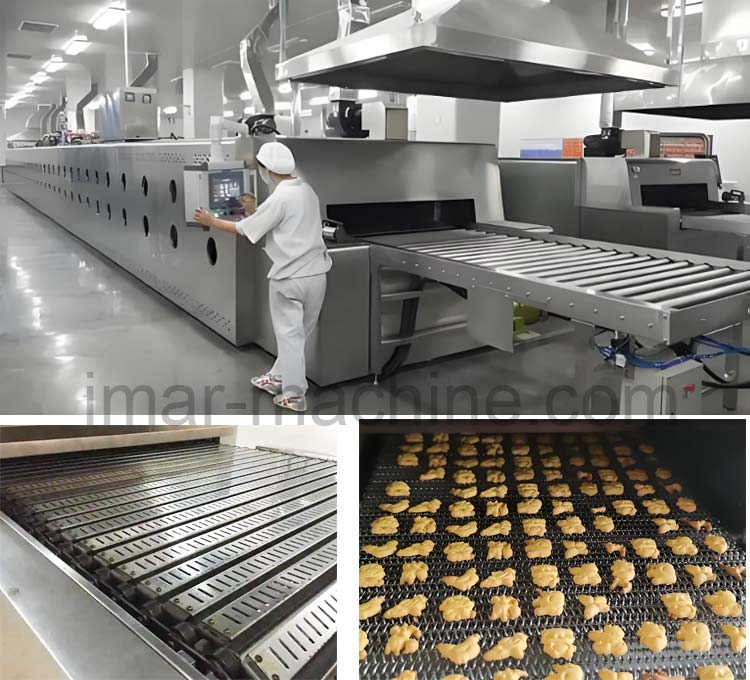
- Key Factors for Selecting an Industrial Baking Oven Supplier
Choosing the right supplier is as critical as selecting the oven itself. Here’s what to evaluate:
Experience and Industry Expertise: Opt for a supplier with a proven track record in your specific industry. An experienced partner will understand your challenges and recommend solutions tailored to your application.
Product Range and Innovation: A diverse product portfolio indicates a supplier’s ability to adapt to evolving technologies.
Quality and Certifications: Verify that the supplier adheres to international standards (e.g., ISO 9001) and that their ovens carry relevant certifications. Ask for case studies or client testimonials to gauge real-world performance.
After-Sales Support and Service: A reliable supplier offers comprehensive post-purchase support, including installation, operator training, spare parts availability, and 24/7 technical assistance. Prompt service minimizes downtime — a critical factor in production environments.
Sustainability Initiatives: In an era of eco-conscious manufacturing, partner with suppliers committed to sustainability. This could include using recyclable materials, reducing emissions, or offering energy-efficient upgrades.
Video of Industrial Baking Tunnel Oven:
Choosing an industrial oven and its supplier is a decision that will impact your business for years to come. With nearly 20 years of experience exporting industrial baking equipment, we at Imar Machine are able to prioritize efficiency, quality, and long-term partnerships. Choosing us is not just buying equipment, but investing in a strategic ally to help your business thrive in a competitive market. Remember, the cheapest option is not always the best; look for a supplier who aligns with your values, understands your needs, and is committed to your success. Make the right choice, and your industrial oven will become the cornerstone of your production excellence.
The global soda biscuit market is experiencing unprecedented growth, driven by consumer preferences shifting toward healthier snacking options. According to a report by Market Research Future, the soda cracker industry is expected to grow at a compound annual growth rate of 7.8% by 2030, driven by the growing demand for low-sugar, high-fiber and clean-label products. As disposable incomes rise in emerging economies, convenient foods like soda crackers are becoming a must-have in people’s kitchens.
However, meeting this demand requires more than just recipes, but also precision, efficiency and scalability in production. Manual operations often lead to inconsistencies in texture, thickness and baking quality, which directly affects brand reputation. This is where advanced soda biscuit processing machine becomes indispensable. We IMAR Equipment offers complete soda biscuit processing machine. By automating mixing, laminating, forming and baking, manufacturers can achieve standardized production, reduce labor costs, and seamlessly scale their business.
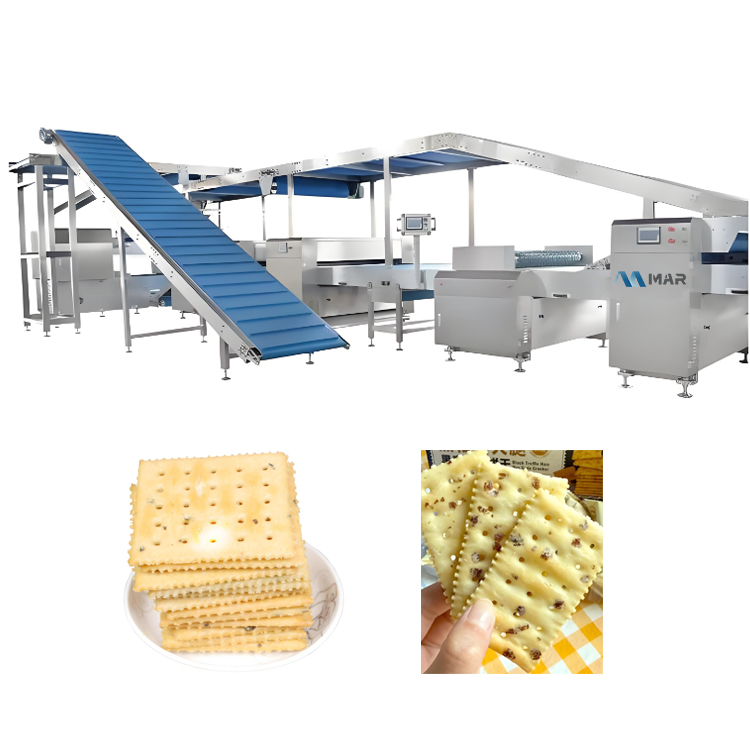
As a trusted supplier of soda biscuit processing machine, we understand the key role technology plays in transforming raw materials into the crispy, golden crackers that the world loves. Let’s explore the excellence of soda biscuit machinery and how to partner with the right supplier to future-proof your business.
What Makes a High-Quality Soda Biscuit Machine?
Investing in a biscuit baking industry is a long-term decision that affects product quality, operating costs, and scalability. Here are the three advantages of a quality machine:
⚪Precision temperature control system
Soda biscuits rely on precise fermentation and baking to achieve their signature crispy taste and fluffy layers. Advanced machines use multi-zone temperature control (accuracy ±1°C) to optimize dough relaxation, layering, and baking. For example, uneven heat distribution can cause cracks or underbaked centers – and our tunnel ovens eliminate these problems by adjusting the temperature in real time based on humidity sensors.
⚪Customizable molds
High-quality machines offer interchangeable molds to meet the needs of different thicknesses (1-5 mm) and designs (diamond, round, or branded shapes). Modular mold systems can be quickly changed without downtime, allowing producers to easily diversify their product lines.
⚪Energy-saving design
Modern machines have integrated heat recovery systems that can use waste heat to preheat dough or heat equipment, reducing energy consumption by up to 25%. In addition, the servo drive motor reduces power consumption by 30% compared to conventional gear systems, ensuring that energy-saving and consumption-reduction targets are met.
Video of Soda biscuit production line:
Why Partner with IMAR Machine? Core Competencies of a Trusted Supplier
Choosing the right machinery supplier is not just about technical specifications, but also about collaboration, expertise and reliability. Here are our advantages:
20+ Years of Industry Leadership
With more than two decades of experience in baking equipment manufacturing, we have continuously refined our solutions through cooperation with global giants such as Garden, Britannia, etc. Our equipment has produced billions of cookies in more than 20 countries, and its durability and excellent performance are trusted by customers.
Tailor-made solutions to meet the needs of all sizes
Whether you are a startup or a multinational company, our equipment can meet your needs. Our flexible line processing capacity ranges from 200 kg/hour for niche artisanal brands to 2000kg/hour for mass-market enterprises. Our engineers will customize the workflow without compromising speed.
Trustworthy Certifications
Compliance is crucial in food production. Our machines have CE, FDA and HACCP certifications, ensuring compliance with hygiene, safety and traceability standards. From easy-to-sterilize stainless steel surfaces to allergen isolation solutions, our designs always keep food safety in mind.
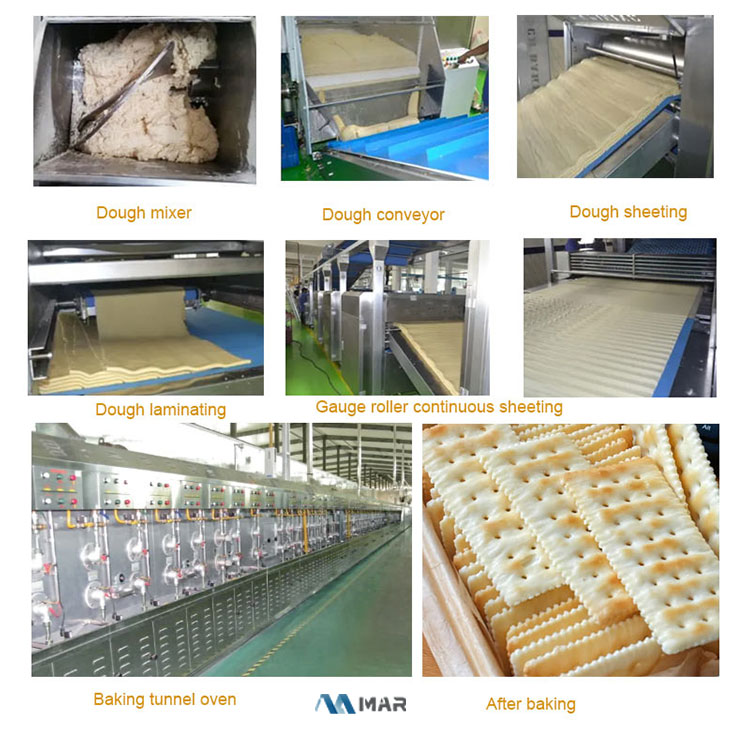
Solving Your Biggest Challenges in Soda Biscuit Production
Even with the best recipes, producers face persistent hurdles. Here’s how we tackle them:
Problem 1: Inconsistent Dough Elasticity
Variations in flour quality or humidity can ruin dough structure. Our patented kneading technology uses real-time viscosity sensors to adjust mixing speed and water ratios, ensuring uniform gluten development every time.
Problem 2: Fragile Finished Products
Brittle biscuits often result from improper baking or cooling. Our humidity-adaptive baking tunnels maintain optimal moisture levels during cooling, while anti-vibration conveyor belts prevent breakage.
Problem 3: High Energy Bills
Traditional ovens waste energy. Our AI-powered Energy Saver Mode analyzes production schedules and automatically switches to idle during low-demand periods, slashing costs by 18–22%.
Beyond the sale: Lifetime support for ongoing success
Our commitment begins when the machine is installed—not ends.
Comprehensive training and maintenance
We provide free on-site training for operators and technicians, covering troubleshooting, sanitation and minor repairs. Customers also receive a personalized annual maintenance plan, including wear diagnostics and software updates.
Case study: 30% reduction in downtime
A Middle Eastern customer was experiencing frequent breakdowns due to desert dust clogging their motors. After implementing our modular airflow redesign and scheduled filter changes, their annual downtime was reduced from 14 days to 9.8 days, saving $220,000 in lost production.
Ready to Boost Your Production? Let’s Build Your Success Story!
The soda biscuit market waits for no one. Whether you’re upgrading existing lines or launching a new brand, our team is here to help you produce faster, smarter, and greener.
Act Now and Unlock Exclusive Benefits:
🎁 Free Production Line Audit: Our experts will identify efficiency gaps and recommend solutions.
🎁 Limited-Time Bonus: The first 20 inquiries receive a VIP Maintenance Handbook and 10 Proven Soda Biscuit Recipes (including low-carb and vegan options).
Contact us today to schedule a consultation. Together, let’s turn your vision into the world’s next favorite soda biscuits!
IMAR EQUIPMENT CO., LTD
ADDRIESS
No.6 Yingxin Road,longdong street,Tianhe district, Guangzhou
imar@topbakings.com
PHONE
+86 13027764560